Low Production Costs with Advanced automotive wire harneses
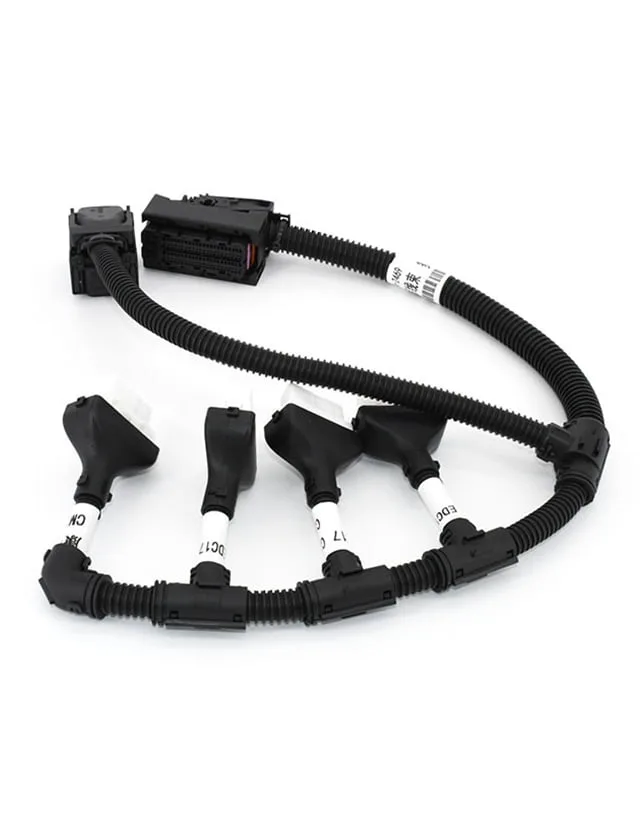
Today's automotive wire harneses are made to be better and cost less money. Best automotive wire harneses, like ISO cables, oil gas sensor types, truck engine wires, and forklift engine automotive wire harneses are top picks. These strong wire harnesses can work in hard places like busy roads or factories. They help your car or machine run more smoothly, use less fuel, and not break down easily. QL-Custom Technology Ltd. sells these harnesses at great low prices so you can save money and still get the best. Save Big & Work Fast With Car Wire Harnesses A automotive wire harneses is like a group of smart wires that work together inside a car. These wires send power and messages to every part. They help parts like lights, screens, and engines talk to each other. Without a wire harness, your car won't work. Our automotive wire harneses are made to help you work faster and better. They are strong but light. They don't break in heat or cold. They allow you to build cars, trucks, and machines in less time. They are made to fit your work just right. That means you save time and money, too. Car Wire Harness: Vital for Vehicles A automotive wire harneses is a bunch of wires tied together neatly. It helps the car run by giving power and sending signals to parts like the engine, doors, seats, and lights. It keeps the wires in order so they don't get messy or broken. It makes the job safer. It also makes building and fixing much easier. Our custom wiring harness is made to fit your car or machine. That means no guesswork. It just works. Gives power to all parts of the car Keeps wires neat and clean Helps build cars faster and safer Lowers...
Read More »Buy custom wire harness for cars: Top qualities available
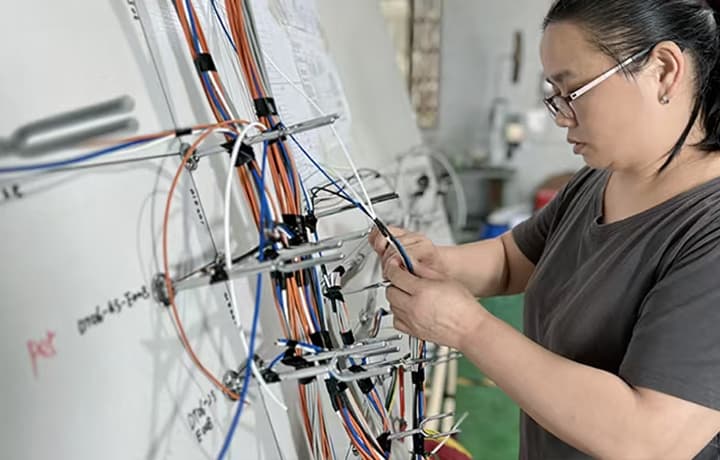
When you are fixing or improving your car, you need a strong custom wire harness for cars that are strong and easy to use. These wire harnesses are essential because they connect parts like lights, the power system, and music parts. They help everything work together safely and smoothly. Different custom wire harness, such as DIN and Mini DIN cables, XLR connectors, flat ribbon wires, and battery plug types are made to be strong and to work well for a long time. All these cables have been tested to make sure they work well. You can find them at QL-Custom Technology Ltd., a company known for giving people good quality items. Low Cost Car Wire Harnesses Matters Much A custom wire harness is a big group of wires tied together and placed inside your car. These wires help carry power and signals from one part to another. They ensure the lights, engine, air conditioning, and radio work correctly. If the wire harness fails, the car can stop working or become unsafe. That is why it is super important for all vehicles to have a good, strong, and low-cost wire harness. Making these custom wire harness can sometimes cost a lot of money. But today, companies use innovative ideas and tools to lower that cost. Wire makers now use better wire plans, faster machines, and simple designs that help make the wires both strong and cheap. Each custom car wiring harness is made to last long and work great without spending too much. Most people now ask for custom wiring harness for cars that are easy to install, repair, and built to last a long time. Things that Makes a Great Wire Harness Reliable A strong custom wire harness is made with tough wires and quality parts. These wires...
Read More »Low Vehicle Weight: Lightweight automotive wire harneses
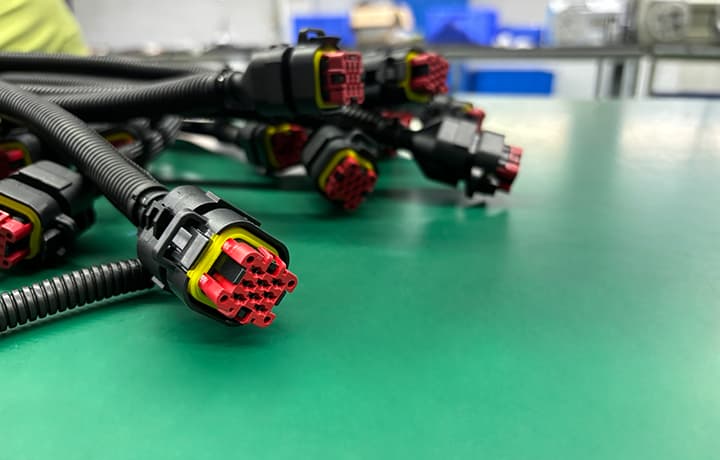
Cars need light to move faster and use less fuel. That's why light automotive wire harneses help a lot. We make strong, light harnesses perfect for engines, sensors, and more. Use oil gas sensor wires to get better engine readings. Use truck tuning wires to boost your truck power. Try ignition wires to start engines safely and fast. These wires work well in hot or cold weather. They fit easily and last long. You can choose the one that fits your car the best. All are made by QL-Custom Technology Ltd. with care. Facts About Lightweight Automotive Wire Harneses These days, every car, every truck, and even every van should be as light as it can be. When a vehicle is too heavy, it uses a lot more gas. If it is an electric car, the battery runs out very fast. But when the vehicle is made lighter, it can travel much farther, using less fuel or power. This saves money for the person who drives it. It also helps the planet stay clean because less fuel means less pollution. One hefty part inside almost all vehicles is something called a wire harness. This part is a big bunch of wires all wrapped together. It connects to everything, like the lights, the engine, the radio, and power windows. These wires help every part of the car talk to each other and do what they should do. If we make this wire harness much lighter, the whole car becomes lighter, too. This makes the car better in many, many ways. Wire Harness Makes Cars & Trucks Heavy A wire harness is like a big bundle of wires covered in something to keep them safe. These wires go to many parts of the car or truck. They send power and...
Read More »Precision-Engineered Custom Wire Harness Solution Service

Custom Wire Harnesses help power move through machines. They keep wires in place and make things run right. Our wire harnesses are just for your tools, cars, or machines. We make them strong and safe, so they work every day without problems. You can get waterproof Custom Wire Harness for wet jobs or overmolded harnesses for extended use. Overmolded wires have covers to stop damage. Panel mount plugs fit tight and work great for many uses. We check every wire to ensure it works well before sending it to you. You can choose the size, shape, and look of the harness. All these are made by QL-Custom Technology Ltd. with care and skill. Easy-to-Understand Custom Wire Harness Solutions Every car, truck, machine, or tool needs wires. These wires carry power and signals from one part to another. A wire harness is a group of cables held together neatly and safely. It keeps wires from getting damaged or moving around. If the wire harness breaks or gets loose, the whole machine can stop working or have big problems. That's why using a strong, safe, and brilliant wire harness made just for your needs is so important. At QL-Custom Technology Ltd., we are proud to build special wire harnesses made just for you. We take time to talk with you and learn about what you need for your job or your project. We make sure your harness fits just right and does the job well. Our team works hard to give you the best quality, fast support, and helpful service from beginning to end. We help you save time, reduce costs, and ensure your machines and vehicles work longer and better. Custom Wiring Harness: Vital for Machines A Custom Wire Harness is a group of wires bundled together using tape,...
Read More »Thermal Management Automotive Wire Harneses for Industry 4.0
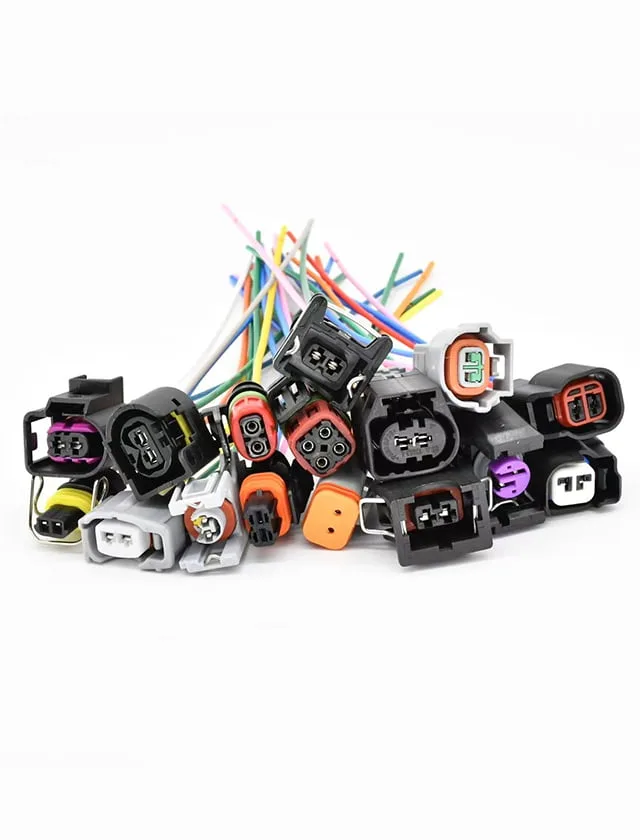
Thermal Management Automotive Wire Harnesses Electric cars, smart trucks, and machines get hot when they run. Wires inside them also get hot. That’s why thermal Automotive Wire Harneses are so helpful. They stop heat and keep the system safe. These bright and strong wires help your machines work better without any danger from heat. They are suitable for sensors, engines, and more. QL-Custom Technology Ltd. has strong ones like ignition pigtails, sensor pigtails, and ISO wire harnesses. You can use them to make your system work better and last longer. Thermal Management in Car Wires Modern cars use a lot of wires to help all their parts work the right way. These wires carry power and signals to the engine, lights, air conditioning, and sensors. But when these wires carry a lot of power or sit too close to parts of the car that get very hot—like the engine or exhaust—they can get too hot themselves. If the wires get too hot, the outer cover can melt, and the wires inside can break or stop working. In some bad cases, this can cause the car to stop running or even catch fire. Thermal management is a way to stop car wires from getting too hot. This helps the wires stay safe, last longer, and do their jobs properly. A car with good thermal management in its wires will work better and have fewer problems. At QL-Custom Technology Ltd., we make special automotive wire harneses built to handle high heat. We use strong and trusted materials. We also test every wire to make sure it will not overheat. We design wire harnesses for all types of cars and trucks, and every automotive wire harneses is made with great care so your vehicle stays safe, even in harsh conditions. Hot...
Read More »High Transfer Rate Custom Wire Harness
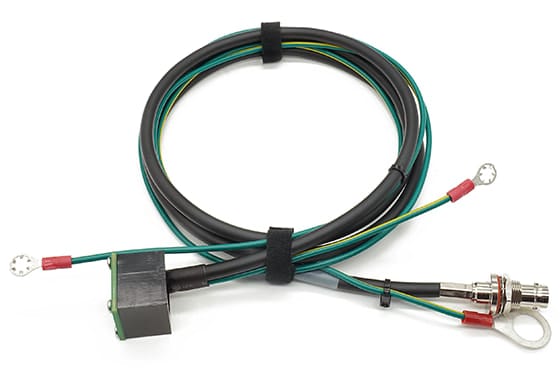
High Transfer Rate Custom Wire Harness When you use machines, cars, or other tech tools, you need safe, fast, and strong wires. That's where custom wire harnesses help. They are made to match your needs. These wires carry power and data quickly and work well in any job. QL-Custom Technology Ltd. has many options to choose from. You can get DIN & Mini DIN connector cables, waterproof cables from M5 to M19, Omron switch cables, and OBD connector wires. They are all made to last and easy to use. High-Speed Custom Wire Harnesses A high-speed custom wire harness is a special group of wires made to quickly and safely move data. These wire harnesses are used in many machines, tools, and systems that need fast and clean signals. They help stop signal problems and make sure everything works right. They are built with strong wires covered with tough, protective outer layers. These are the exact harness for preventing the heat and other weather odds easily. These cables last for a long time. Top features: Breakneck speed. Clean and strong signals. Built with strong materials. Works for a long time. Easy to install and use. Made to fit your job needs. DIN & Mini Din connector cable DIN and Mini-DIN cables are round-shaped plugs that are used with music tools, old video devices, and some machines in factories. Even though they look small outside, they carry many wires inside. These cables are great when you want to save space but still need many wires to do the job. We make custom DIN cables just the way you want them. We can make them long or short, thick or thin. We can use different wire colors to help with setup. We also add shields to stop outside noise or...
Read More »Low pressure molding material and Services for electronics

Tiny parts in electronic tools, like wires and chips, are easily damaged. If they get wet or hit, they can break. If one part fails, the whole device may stop working. Low pressure molding materials helps protect these parts. This process uses soft, hot glue-like Low pressure molding materials that cover the parts gently. It fills the empty spaces, blocks out dirt and water, and strengthens parts. It is also fast and clean. QL-Custom Technology Ltd. offers complete molding services. They use strong and trusted Low pressure molding materials like Technomelt. They work on PCBs, USBs, LEDs, and even sensors. Their molding work is quick, safe, and looks great. Low Pressure Molding Material: Protect Small Electronics Low-pressure molding is a soft and gentle way to cover and protect small electronic parts. It uses a special type of melted plastic. This plastic flows slowly and wraps around the small piece without pushing hard. It fills every little space, and then it cools down very fast. After it cools, it becomes hard and strong. This makes a shield around the part, keeping water, dirt, heat, and damage away. This method works well for small, delicate items like LED lights, wires, chips, and sensors. Because low pressure and low heat are used, your tiny parts do not get broken or moved. The parts stay in place and look clean. Many companies like this process much better than glue, tape, or high-pressure methods. It is quicker, neater, and safer. Your parts look better and last longer. Low pressure molding material: Technomelt hotmelt resins At QL-Custom Technology Ltd., we use Technomelt hotmelt resin for our work. This is a top-quality material, a well-known company that makes safe and strong products. This resin is great because it melts easily and flows like syrup....
Read More »Chemical-Resistant Custom industrial cables for Oil & Gas
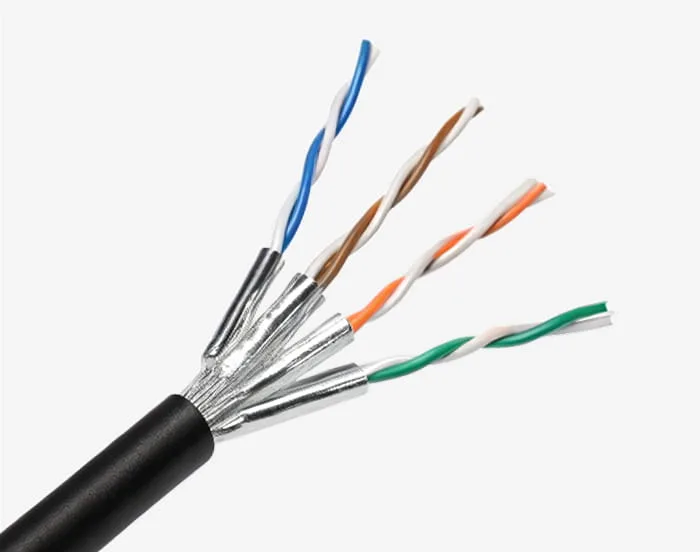
Working in oil and gas means facing strong chemicals, heat, and harsh environments. Regular cables can't survive there. You need custom industrial cables that resist chemicals and last a long time. QL-Custom Technology Ltd. makes special custom industrial cables for this. Their CAN Data Cable sends data fast. CMP fire-resistant wires help stop fires from spreading. High-Speed Transmission Cables are quick and decisive. Drag chain cables can move a lot and still stay safe. These wires are made to be strong, safe, and chemical-proof. They work well even in the hardest places. Tough & Safe Cables in Oil and Gas Projects Oil and gas work happens in some of the hardest places on earth. These places are often very hot or very cold. There is a lot of water, salt, and oil. The ground might shake. Heavy machines move. And dangerous chemicals are everywhere. People work on deep-sea oil rigs, in desert pipelines, and inside hot factories. In these places, regular cables do not last long. They can melt, break, or stop working. If a cable breaks, machines stop, work stops, and people could get hurt. Fires can even start. That's why using the correct cable is so important. We make strong and smart custom industrial cables. These are not regular cables. These are chemical-resistant cables made to stay safe and strong in tough places. These are also called custom electrical cable assemblies. We build each cable to match your job. It will fit your machine and your space just right. This means less trouble and more safety. Right Cable That Fights Chemicals In oil and gas, custom industrial cables have to face many bad things—things like strong fuels, acids, saltwater, dirt, and heavy shaking. If you use standard cables, they can swell, snap, or stop sending power....
Read More »Automotive wire harneses Thermal Management
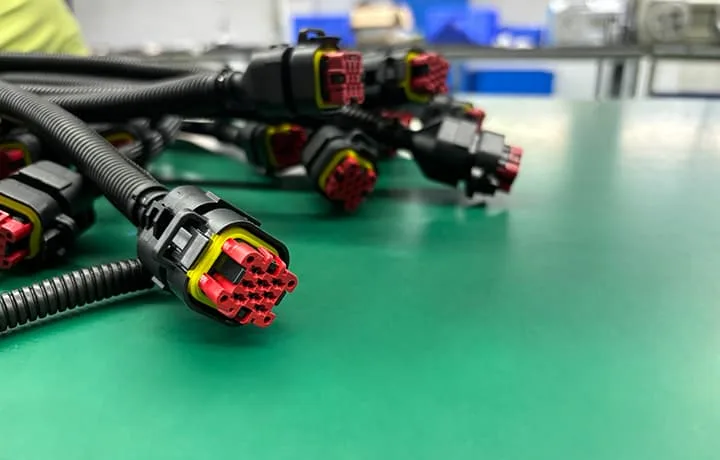
The engine in a car gets very hot when it runs. If the wires near the engine are not protected, they can melt or burn. Melted wires can stop the vehicle from working or even cause a fire. You need Automotive wire harneses that can handle high heat to keep your car safe. QL-Custom Technology Ltd. makes special Automotive wire harneses that are heat-safe. The Forklift Engine Harness is strong and reliable. Oil and gas sensor wires are made for hot work areas. Their ignition pigtails are well-covered and protected from heat. These wires are made with insulation and heat-shield materials. They keep the car working and reduce repair needs. Keeping Car Wires Cool Is Important When cars are running, they create a lot of heat. The engine, exhaust pipes, and brakes make high heat levels while working. This heat spreads throughout the whole engine area. Wires that are close to these hot parts can quickly become too hot. That is not safe for your vehicle. If a wire gets too hot, the soft plastic coating around it can melt. Once the cover melts, the wire inside might stop working, which can cause the car to stop or even lead to sparks. Those sparks could start a fire. That's why keeping your car's auto harness wires cool and safe is super important. We use special materials like heat wraps, fire sleeves, and protective shields to stop this heat from harming wires. These are special blankets for your harness cables that keep the heat away. These covers block the heat before it touches the wires. This helps the cables stay in good shape for longer. It also keeps the car safe and working well. This is not just useful for standard cars. It also helps heavy vehicles like trucks, forklifts,...
Read More »Custom wire harness for Robotics: Flex-Life & Strain-Relief
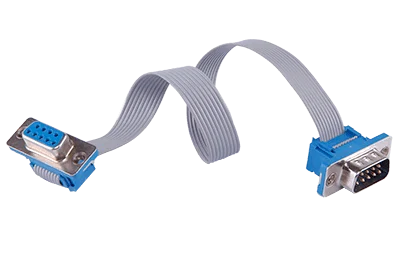
Robots move a lot while working. Their cables twist, bend and turn again and again. If the cables are weak, they can break easily. That stops the robot and causes problems. You need strong, flexible wires that can move without breaking to avoid this. QL-Custom Technology Ltd. makes Custom wire harnesses that work great for robots. Their custom XLR cables are thick and safe. Flat Ribbon cables are thin and can bend many times. Sensor cables are great for sending fast signals. Overmolded wires are sealed and protected to last longer and stay clean. These cables are built to handle movement and stress. They help robots keep working without needing many repairs. This saves time, effort, and money too. Robots Need Custom Wire Harness So Much A custom wire harness is a group of wires for your robot or machine. These wires are put together smartly. They help move power and signals from one part to another part. When wires are grouped like this, they are much safer. They are also easier to use, easier to fix, and easier to keep clean. A Custom wire harness helps your robot work much better. It keeps the wires neat and tidy. This also helps save space inside the robot or machine. The wires are cut to the correct length and shaped to fit just right. They go exactly where they need to go. That makes building and fixing your robot or machine much easier and faster. Custom wire harnesses are made to be very strong and long-lasting. They do not break or come loose easily. They stay where they are supposed to be. They make your robot's job easier. No extra wires are hanging around. Everything is set up to help your robot work fast, safely, and well. ...
Read More »