JAE Connector series, types, uses, and price
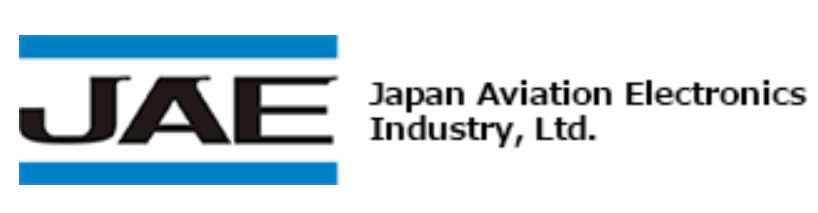
JAE Connector series, types, uses, and price What is JAE? JAE is Japan Aviation Electronics Industry, Ltd. Is a company focused on providing connectors for various application types. Features and applications of JAE connectors JAE connectors penetrate a very wide range of industries, automobiles, aviation, smart phones and other small equipment are involved. Its products are highly recognized by customers for their high density, high reliability, water and dust resistance, especially in the automotive and aviation fields. Types of JAE Connector According to the official description, there are roughly ten types of JAE connectors as follows: External interface connectors: used for the connection between different devices and systems, can meet various standards according to customer needs. Board-to-board connector: used to connect PCB. Various stack heights, poles and contact spacing can be designed according to product requirements. Board-to-board FPC/FFC connector: used for the connection between PCB and FPC or FFC. And same to the previous board-to-board connector, it can also have a variety of different stack heights, poles quantities and contact spacing according to product requirements. Board-to-wire connector: used for connection between PCB and cable. Round connectors: This type of connector is usually very well sealed. Square-shape connector: This type of connector can often be used in multi-PIN connection design, which can efficiently use wiring space to improve transmission efficiency. Optical fiber connector: used for high-speed, high-bandwidth data transmission and communication. This kind of application generally have the characteristics of high anti-interference. Coaxial cable connector: used to connect coaxial cables. Relay connector: It acts as a link in the circuit. Memory card connector: used to connect SD and SIM cards, there is a variety of different card insertion and withdrawal methods according to customer needs. Memory module connector: It needs to be compatible with memory module standards, such...
Read More »Which Certificates Wire Harness Involved?
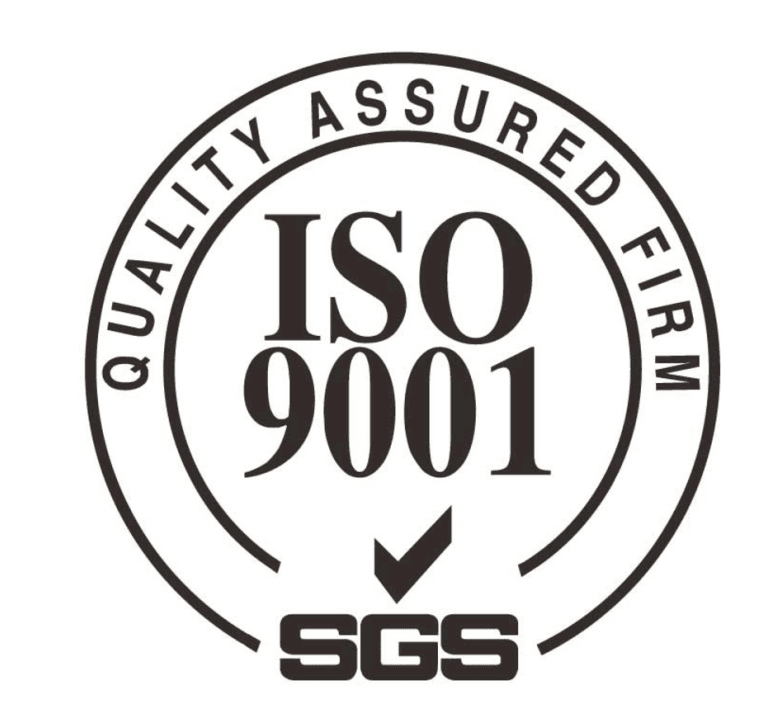
Which Certificates Wire Harness Involved? In the increasingly competitive wire harness market, product certification and factory certification shows particularly important, through the professional testing organizations to carry out strict quality control of product quality, you can effectively screen out qualified products, as well as high-quality suppliers, is a kind of protection for customers. 1- Product Certification RoHS 1. RoHS certification is a mandatory standard developed by the European Union. It is mainly used to regulate the material and process standards of electrical and electronic products, so that it is more conducive to human health and environmental protection. Rohs has been incorporated into the EU mandatory certification CE, generally only require a test report on it, but if the customer needs a certificate, you can also issue a CE certificate. It is mainly for the raw material of the product to be certified. Reach 2-Reach is only a test report, there is no certificate, REACH certification is the EU regulation “Registration, Evaluation, Authorization and Restriction of Legal Goods”. It is mainly for the raw materials of the product to be certified. Water-proof 3-Waterproof certification: First, we need to find out is the customer requirements of the material itself waterproof or design and manufacture of waterproof, which is our priority. About the material itself waterproof: the material itself waterproof means that the connector or wire and cable material can be used outdoors, will not be in the case of immersion in the physical deterioration. Manufacturing design waterproof: It means that after this product is designed and manufactured, this design will not enter water or dust, such as our common strain relief design. UL 4-UL: U.S. Security Laboratory certification, proving that the product meets U.S. safety standards. UL is mainly for North America, out of the U.S....
Read More »The design logic of Coiled Cable

Coil Cable Design, Manufacturing, Length Calculation and Precautions 1. What is a Coiled Cable ? A Coiled cable, also known as a retractable coiled cord or spiral cable, is a type of electrical cable that can stretch and retract like a Coils. The prototype of the coil cable is actually a straight cable. The straight cable is wound around a fixed-size jig rod by winding, and the clamps on both sides are used to clamp the wire. Then it is put into the oven and baked for a certain period of time. It is taken out to form a coil cable. 2. Calculating the Real Length of a Coiled Cable 1. Determine the Structure: Understand the number of coiled sections and straight sections that make up the Coiled cable. 2. Measure the Coil Parameters: Coil length: we need to be clear the coiled part length, from one pc coiled cable L=350mm Coil ID : Measure the coiled part OD=15mm this parameter determines the fixture stick’s OD Coil OD: Measure the coiled part OD=25mm Cable OD: Measure the cable OD5.0mm Then we can work out the cable coiled part how many coils. Use the coiled part length/Wire OD 350/5.0=70coils Counting 1 coil length = πD= 3.14 X (25mm-5.0mm)=62.8mm (‘cause we can’t use the max OD to count the Circumference ) 1 coil 62.8mm X 70 coils = 4396mm+the both ends lengths is the one pc cable real length Note that the measurement method is relatively simple and intuitive but may have some errors. The formula calculation method requires accurate measurement of the structural parameters of the Coiled cable, and the calculated result is only an approximation. In practical calculations, choose the appropriate method based on the specific situation. 4. The...
Read More »The key point of quality control of wire harness IPC620
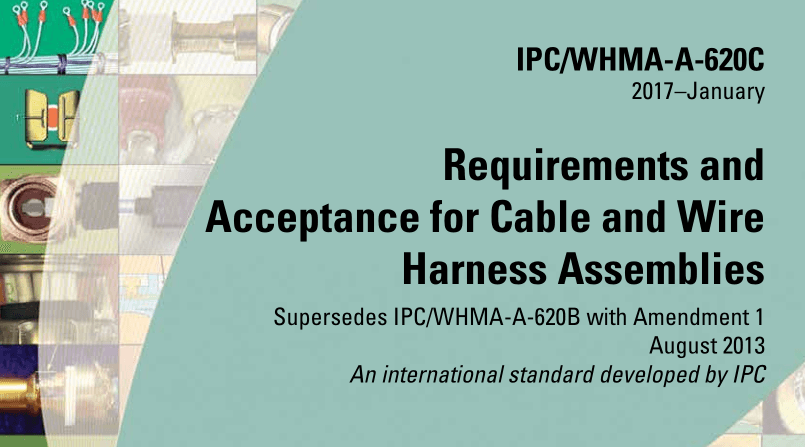
The key point of quality control of wire harness IPC620 Contact us to get IPC620 english version printed book I. Processes Involved in Wire Harness Manufacturing The processes involved in wire harness manufacturing include but are not limited to: Cutting: Refers to cutting electronic wires or cables to the required length using machines or manually, without damaging the insulation or outer sheath. Outer Sheath Stripping: The outer sheath usually refers to the cable sheath. The outer sheath stripping machine should not scratch or cut the insulation of the core wires when stripping the outer sheath. Any cuts, breaks, cracks or splits in insulation (not shown). u Insulation thickness is reduced by more than 20% . u Uneven or ragged pieces of insulation (frays, tails, and tags) are greater than 50% of the insulation outside diameter or 1 mm [0.039 in] whichever is more . u Insulation is charred . u Insulation is melted into the wire strands . Core Wire Stripping: Adjust the core wire stripping machine to the required size for stripping, and be careful not to scratch or cut the copper wires. Crimping: Select the appropriate blade according to the terminal size. Crimp the prepared wire with the terminal crimp part using the blade, ensuring a firm crimp and that the appearance and pull force of the crimped terminal meet the standards. Put on connector: Insert the qualified crimped terminal wires into the matching connector housing. A clear click sound will be heard when the connector is fully inserted. Wire Twisting: Adjust the wire twisting machine to the appropriate height to ensure that the copper wires are not flattened or tangled, and the twisted conductor is in a uniform spiral shape. Tinning: Apply flux to the prepared...
Read More »How we build wire harness drawings ?
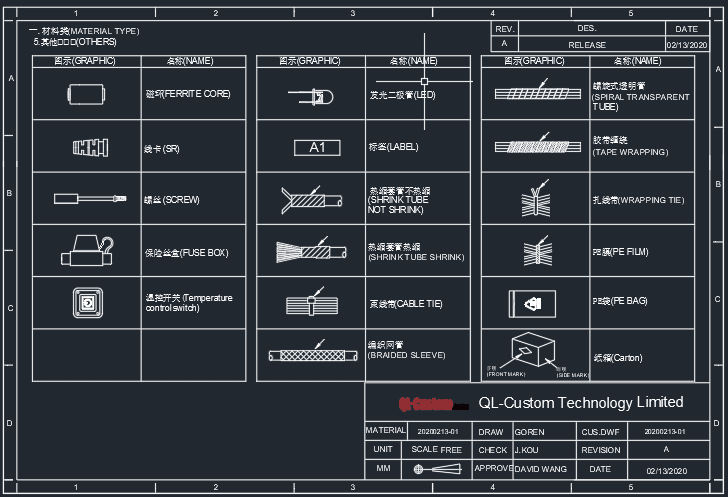
Overview of the Necessity and Importance of Wiring Harness Drawings Build Wiring harness drawings are essential for providing a clear and detailed representation of the harness layout, connection relationships, and component information. These drawings ensure the accuracy, reliability, and safety of the wiring harness. They illustrate the harness routing, including starting points, endpoints, and intermediate connection points, as well as the harness path. Moreover, the drawings depict the connection methods and relationships of each wire within the harness. As the primary source of information for wiring harness production, these drawings play a fundamental and critical role in the manufacturing process. Wire harness drawings build from customers' drawings : QL-Custom's Process from Inquiry Receipt to Drawing Submission for Customer Review : Upon receiving an inquiry, including customer drawings or samples, our engineers determine the sourcing strategy, whether it's original or domestic materials. They then source quotes from multiple suppliers, comparing prices to offer the best option to the customer. After price confirmation, a sample request is submitted. Engineers create drawings based on customer-provided information or samples. After internal review and approval, the drawings are sent to the customer for confirmation. Drawing Considerations and Details – Analyze customers' drawing to generate our Drawing : As shown above, a typical drawing consists of seven main sections: Drawing information: Customer part number, internal part number, drafter, reviewer, revision level, date, etc. Revision history: Details of any changes made to the drawing. Quality and testing requirements: Specific standards and tests the harness must meet. 2D layout: A comprehensive view showing component placement, wire lengths, and other crucial manufacturing details. Circuit diagram: Illustrates the point-to-point connections within the harness. Bill of Materials (BOM): Lists all components, including wires, terminals, connectors, and sleeving, with quantities and internal part numbers. Packaging...
Read More »What Plastics Can Be Used for Wire Insulation and Cable Jacketing ?
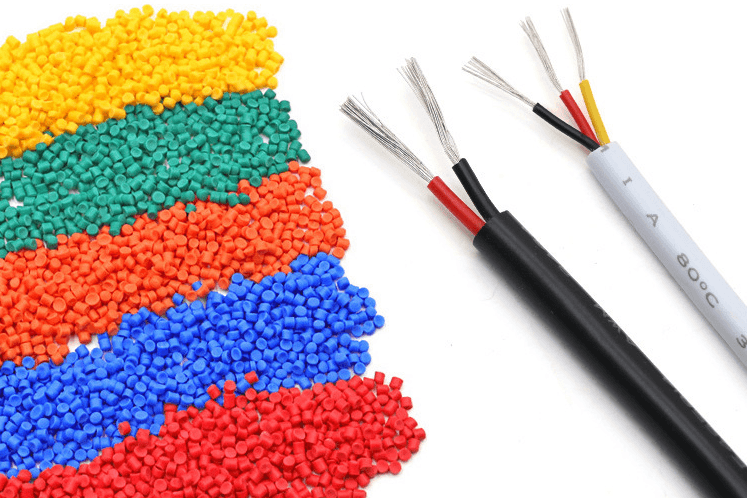
What Plastics Can Be Used for Wire Insulation and Cable Jacketing ? Wire insulation and cable jacketing are essential in electrical applications, meaning that the materials used for them are crucial in ensuring the safety, performance, and durability of cables. So, what plastics can be used as insulation and jacketing materials for wires and cables? Understanding Wire Insulation and Cable Jacketing Definition of Wire Insulation To make good use of wire insulation, we need to know what it is. Wire insulation is a layer of non-conductive material that surrounds a conductor. It effectively prevents leakage and protects the conductor from external environmental factors, avoiding accidents such as leakage, short circuit, and electric shock caused by contact between the internal conductor and the outside world. Definition of Cable Jacketing Cable jacketing is a protective layer that wraps around multiple insulated wires or cables. They are used to protect internal wires from external environmental damage, such as physical damage, moisture, chemicals, and UV radiation. Wire insulation primarily targets individual wires, while cable jacketing can protect multiple wires or cables What Materials Are Used for Wire Insulation? Polyvinyl Chloride (PVC) PVC has excellent electrical properties, good flexibility, and can be used in humid environments, making it one of the most commonly used materials for wire insulation. The price of PVC is very advantageous, which is also an important reason for its widespread use. Cross-linked Polyethylene (XLPE) XLPE itself is not a plastic, but the PE rubber compound is irradiated after extrusion to cross-link its chemical molecules, making it more temperature-resistant after aging. XLPE has extremely high heat resistance. It can withstand higher temperatures. Cables insulated with XLPE can work in an environment of 90°C for a long time. More famously, it can withstand instantaneous short-circuit temperatures...
Read More »Single-core UL and Europe Electronic Wire?
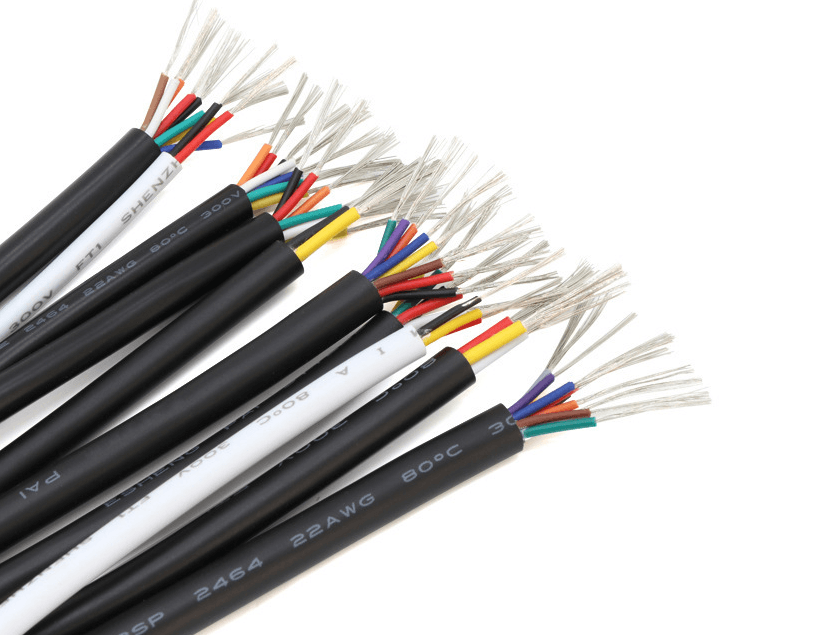
What is single wire ? The term "single core wire" is often heard, but what exactly is it? Let's explore this ubiquitous component, present in almost every aspect of our lives, from its definition and applications to its advantages. A single core wire is an electrical wire consisting of a single conductor encased in insulation. The conductor is typically made of bare copper or copper plated with tin, silver, or nickel. The insulation is commonly made of PVC, but other materials can also be used. The conductor structure can be stranded or solid copper, depending on customer requirements. From simple circuits to complex telecommunication systems, from high-tech products to simple electronic devices used in our daily lives, single core wires are indispensable. The primary difference between single core wires and multicore cables lies in the number of conductors used. UL Standard Single Core Wires UL 1015 - Single Core PVC Insulated Wire Description: Wires using PVC as insulation material are suitable for use in dry locations. Applications: UL1015 hook-up wires are suitable for use in control circuits, appliances, and other electrical equipment. UL 1007 - Single or Stranded PVC Insulated Wire Description: Like the 1015, UL 1007 wire also uses PVC as its insulation material. However, 1007 is designed for use in low voltage environments and is more flexible. Applications: Its flexibility makes it often used for internal wiring of appliances and electronic equipment. UL 1569 (Single Conductor) Description: As the name suggests, a single conductor is composed of a single conductor, using a single or stranded 30~10AWG tinned or bare copper. This conductor is flat and flexible, with less restrictions on the use of space. Applications: Commonly found in electronic equipment, automotive applications, and other specialized uses. European Standard Single Core Wires 1....
Read More »What is FPC FFC Cable?
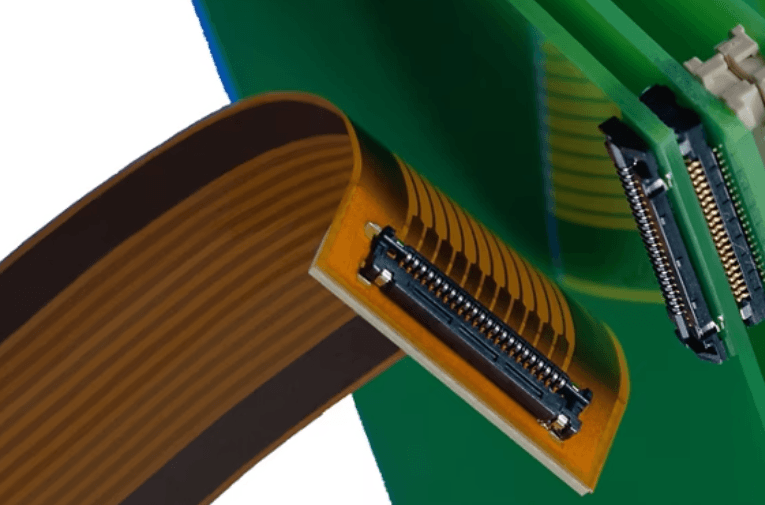
Introduction to FPC and FFC Cables QL-Custom can customize Flexible Printed Circuit (FPC) cables, which can flexibly connect various electronic components. Due to their high flexibility, FPC cables can be used in printed circuit boards, computers, and other space-saving electronic devices. QL-Custom can also customize Flat Flexible Cables (FFC). Similar in application to FPC cables, FFC cables have a different structure. They are in a flat ribbon shape and are suitable for organized wiring solutions. FPC and FFC cables are an indispensable part of electronic devices, ensuring effective signal transmission and connection. Main Differences between FPC and FFC Cables QL-Custom can customize all cables according to your specific needs, whether you need FPC or FFC cables. As mentioned above, the main difference between these two types of cables lies in their structure. The conductors of FFC cables are mainly copper, which is used as the conductor for many wire boxes and cables because of its good conductivity and flexibility. In contrast, the conductors of FPC cables use thinner copper foil or metal sheets, allowing FPCs to be flexibly used in complex designs or in spaces that are more compact. QL-Custom can provide appropriate recommendations on when and where to use FPC cables and FFC cables based on the actual needs of your project. For example, if your application requires high flexibility and compact design, FPC cables would be the better choice. However, if you simply need a straightforward connection, FFC cables would suffice. A good understanding of the differences between these cables makes it easier to make the right choice when selecting the appropriate cable for your electronic project.
Read More »What is Flat Ribbon Cable?
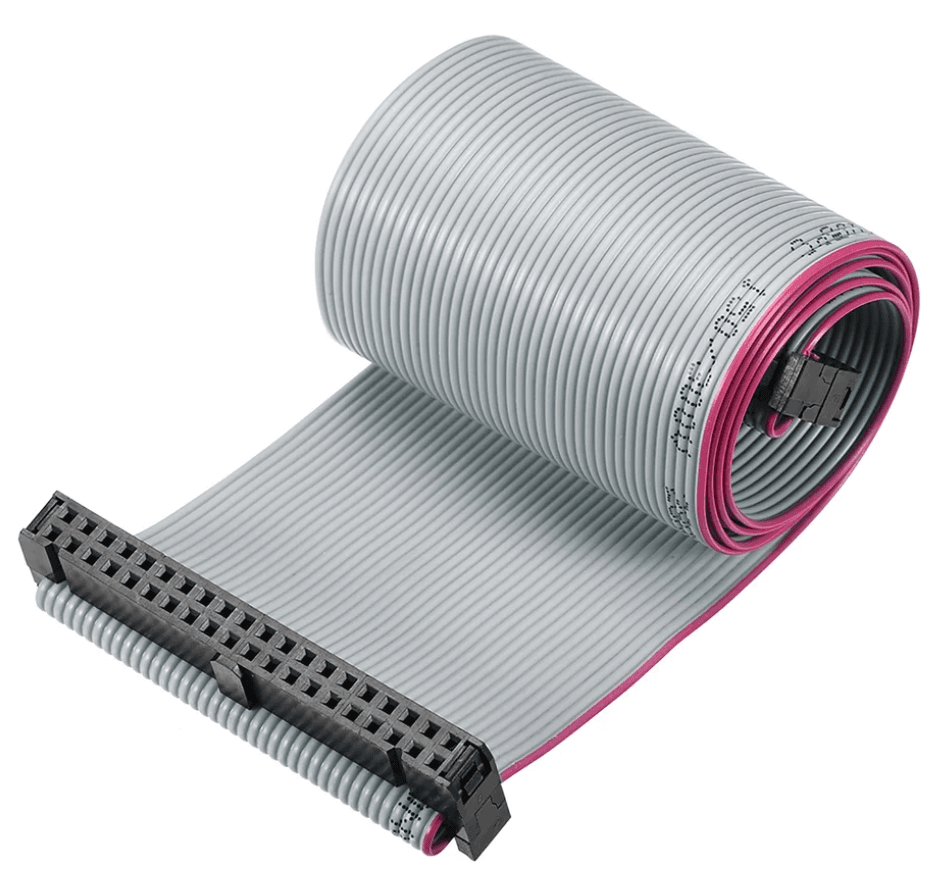
Introduction to Flat Ribbon Cable Flat ribbon cable is usually connected by multiple electronic wires in parallel. This structure could simplify the harness design of the overall circuit and improving space utilization. Flat ribbon cable is generally used in computers, printers and other equipment that require compact and flexible wiring. Therefore, flat ribbon cable is also one of the most common types in QL-Custom customized wiring harness solutions. Types of Flat Ribbon Cables There are different types of flat ribbon cables to suit different scenarios. One of the most common types in QL-Custom's custom cases is the IDC (Insulation Displacement Connector) flat cable harness. Its biggest feature is that the connector can be quickly and easily terminated without stripping the insulation of individual wires, which makes it very time-saving and efficient in production. Another common form of flat ribbon cable is multi-core cable flat cable. Compared with single-core wiring, this type of wiring harness can transmit more signals in the same time and is suitable for more complex data communication and control systems. Like ordinary wires, flat ribbon cable are divided into two types: shielded and unshielded. Compared with unshielded ones, the main function of shielded ones is to prevent electromagnetic interference, which is suitable for electronic equipment and scenarios with high requirements for signal anti-interference. Additionally, flat ribbon cable are generally color-marked. In complex scenarios, different colors help people quickly identify and distinguish wires, thereby reducing the possibility of errors during installation and maintenance. What QL-Custom can do for you QL-Custom can customize different ribbon cable solutions including IDC, multi-core cable, shielded or unshielded cables, and color-marked cables to meet your specific needs. Whether you need customization now or in the future, understanding the above cable information will help you choose the right cable.
Read More »Single Wire vs. Multi Core Cable
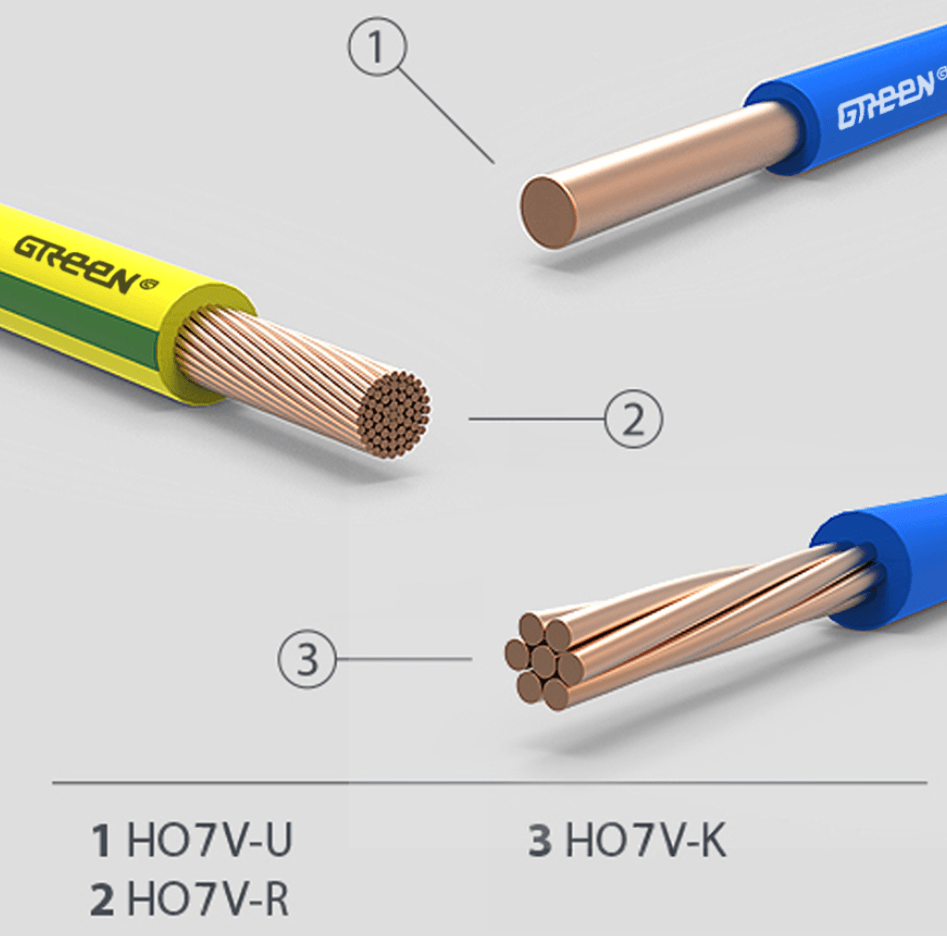
Single Wire vs. Multi Core Cable knowledge base What is single wire? What is multi-core cable? And what are the main differences between them? For friends who need to use wire harnesses in their equipment, it is very necessary and important to figure out these questions. In this article, QL-Custom will explore the characteristics and advantages of Single wire and multi-core cable, and how each type affects performance and different applicable scenarios. Understanding Single wire What is Single wire? Single wire generally refers to a wire with an insulating sheath wrapped around the conductor. The conductor material is usually made of bare copper or alloy copper. Its conductor structure can be a single solid copper or multiple strands of copper wire twisted together. Its common insulation layer materials include PVC, PE, TPEE, silicon, Teflon, etc. Types of Single wire Based on the above different structures of conductor and insulation layer combination, single core wire can be of many types. Examples are as follows: Bare single wire: Wires only made of conductors. It has good conductivity, but since there is no insulation layer, bare wires require special attention to protection during transportation and storage. Insulation Single wire: It is composed of an insulating layer wrapped around a conductor. The main function of the insulating layer is to protect the conductor inside the wire. Common insulating materials include PVC, PE, silicone, TPEE, PP and PFA, FEP, PTFE, which are suitable for different rated temperatures and voltage capacities. Shielded single wire: This type of wire has a shielding layer added between the insulation layer and the conductor. It is a type commonly used in the field of new energy, such as XL-PE double-insulated shielded wire. This type has higher safety and data...
Read More »