Формование под низким давлением
By Tina / 2018年5月19日
Формование под низким давлением
1972 :Франция IBM впервые.
1987 :Eruope automotive начинает производство пресс-форм для электроники
1993 :Использование для Франции автомобильной промышленности жгутов проводов
1995 :Широкое применение в автомобильной промышленности и распространение на электронику
2000 :Используется для печатных плат, сенсорных устройств и разъемов.
После 2000 года: Широкий диапазон использования для мировых предприятий.
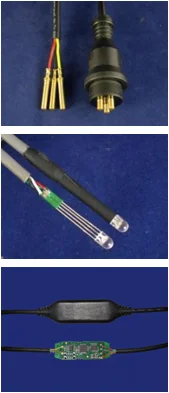
Процесс литья под низким давлением - это упаковочный процесс, в котором используется очень низкое давление для впрыска инкапсулирующего материала в форму и быстрого застывания. Для достижения изоляции, термостойкости, ударопрочности, снижения влажности, водонепроницаемости, пыле- и химстойкости.
Применяется для: печатных плат, электронных разъемов, жгутов проводов, батарей, переключателей, светодиодных ламп, катушек и т.д..
Короткий цикл впрыска
Смола Материалы защита окружающей среды
Состав не нужно смешивать
Термопласты не требуют времени для застывания
Высокая надежность
Простая конструкция пресс-формы
Водонепроницаемый
Изоляция
Устойчивость к ударам
Температурная стойкость
Химическая стойкость
Лом Не наносит вреда окружающей среде
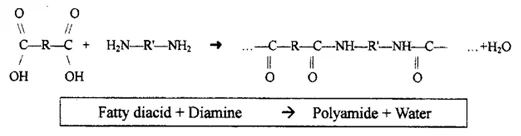
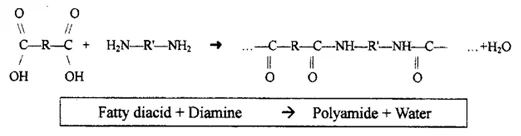
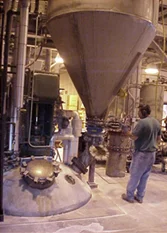
Полиамидоамины на основе димерных кислот образуются в результате
Полиамидоамины на основе димерных кислот образуются в результате поликонденсации диаминов и дибазовых кислот.
Димерная кислота, выделенная из обычных сельскохозяйственных продуктов
Касторовое масло
Кукурузное масло
Льняное масло
Арахисовое масло
Растительное масло
Талловое масло
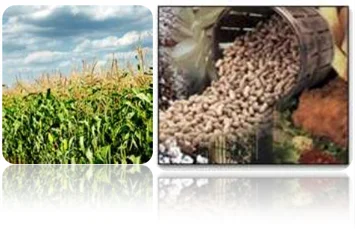
Материал гранулированный В целом черный или янтарный Может быть выполнен в других цветах
Давление всасывания1-200psi(0~60кг)
Температура формовки160° C~230° C
Защитите собственность ИС и компонентов
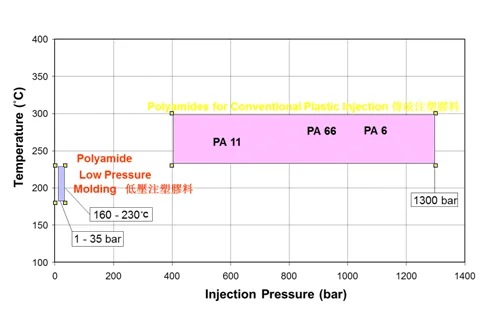
PA/PO/PET/PUR
Достаточный запас QL-Custom
QL-Custom Профессиональная консультация
Энвирметалл
Хорошие изоляционные свойства, огнезащитные свойства и коррозионная стойкость
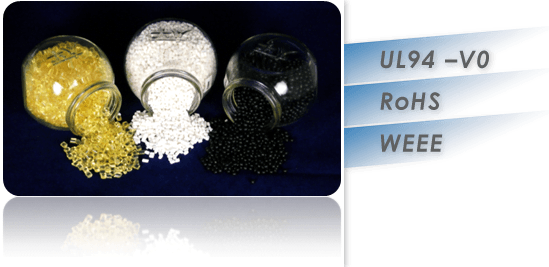
Устойчивость к высоким температурам
PA673 OM673 Используется для автомобильных капотов Янтарь -40℃~140℃ по Шору A 90 187℃ ±5℃
PA678 OM678 Используется для автомобильных капотов Янтарь -40℃~140℃ по Шору A 90 187℃ ±5℃
PA682 OM682 Внутри автомобильной шины, низкая водная трамиссия Янтарный берег A 88 188℃ ±5℃
PA687 OM682 Внутри автомобильной шины, низкая водная трамиссия Янтарный берег A 88 188℃ ±5℃
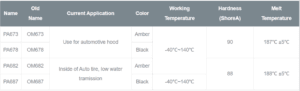
Клей для пластика
PA633 OM633 Используется для автопожарной стены янтарного цвета -40℃-130℃ по Шору A 90 175℃ ±5℃
PA638 OM638 Используется для автопожарной стены янтарного цвета -40℃-130℃ по Шору A 90 175℃ ±5℃
PA652 OM652 Хорошее сцепление и гибкость Янтарь -40℃-100℃ Shore A 77 157℃ ±5℃
PA657 OM657 Хорошее сцепление и гибкость Янтарь -40℃-100℃ Shore A 77 157℃ ±5℃
PA6208 MM6208 Кабельная разгрузка от натяжения янтарная -40℃-100℃ по Шору A 78 155℃ ±5℃
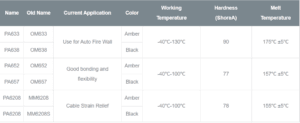
Смолы для повышения прочности
PA341 OM341 Высоковольтные модулиПрозрачный оранжевый -25℃-125℃ по Шору A 92 173℃ ±5℃
PA641 OM641 Memory Stick, разъемы янтарного цвета -40℃-130℃ Shore A 92 175℃ ±5℃
PA646 OM646 Memory Stick, разъемы янтарного цвета -40℃-130℃ Shore A 92 175℃ ±5℃
PA648 OM648 Устойчивость к ультрафиолетовому излучению, электроника на открытом воздухе Черный -40℃-130℃ Шор A 92 175℃ ±5℃
Химическая стойкость
AS4226 -Автомобильный преобразователь, промышленные сборки Прозрачный -40℃-85℃ -165℃ ±5℃
AS5373 MM5375/MM Q-5375 Отличное сцепление с твердыми пластмассами, OvermoldingБелый (не прозрачный) -30℃-100℃ Shore A 55 139℃±5℃
PA2384- температура и маслостойкость, автомобильные датчики янтарь -20℃-175℃ Shore A 65 ~75 189℃ ±7℃
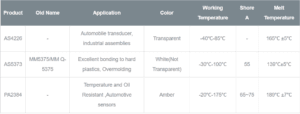
Устойчивые к ультрафиолету пластмассы для литья под низким давлением
PA668- устойчив к ультрафиолетовому излучению, светодиоды и освещение на улице Белый -25℃-130℃ по Шору A 90 155℃ ±5℃
PA6344- УФ-стойкий расплав, пластиковая сварка хорошо скрепляет Черный -20℃-100℃ Shore A 76 147℃ ±9℃
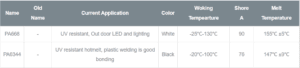
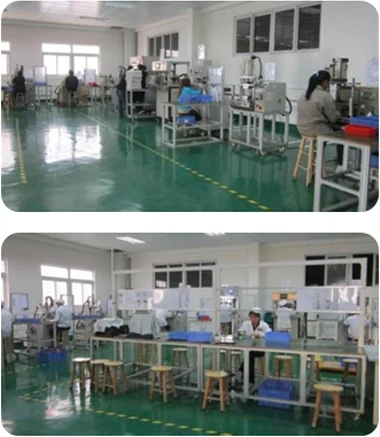
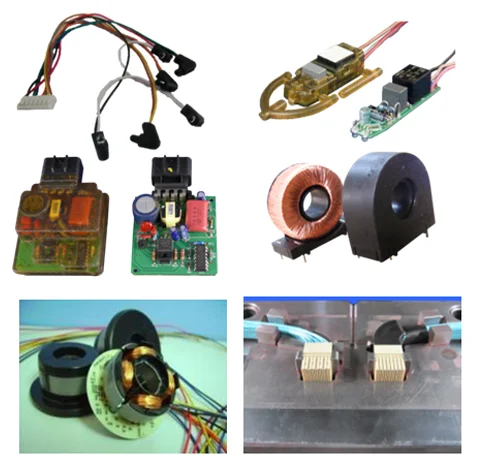
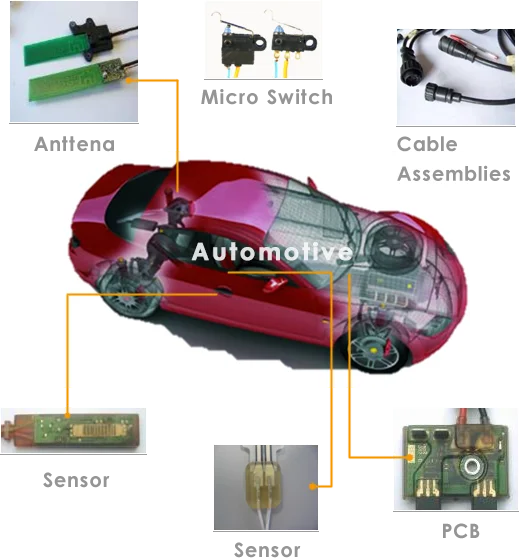

Преимущество инкапсуляции
Преимущество цены машины
Преимущество в цене пресс-формы
Можно вводить прецизионные изделия, потому что:
Низкое давление + низкая температура
Короткий цикл введения продукта
Простая конструкция пресс-формы
Поскольку мы посвятили себя разработке технологии литья под низким давлением
Поскольку мы предлагаем полный спектр решений для впрыска под низким давлением
Потому что мы продвигаем 7 лет с международной технологией литья под низким давлением
Потому что у нас лучшая команда.
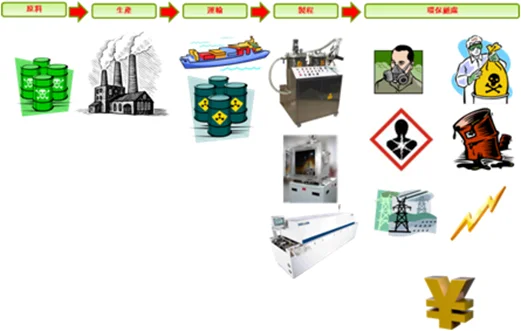
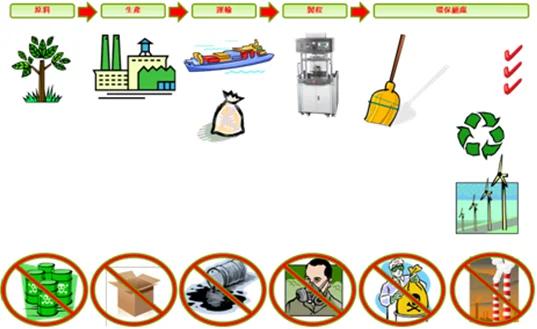